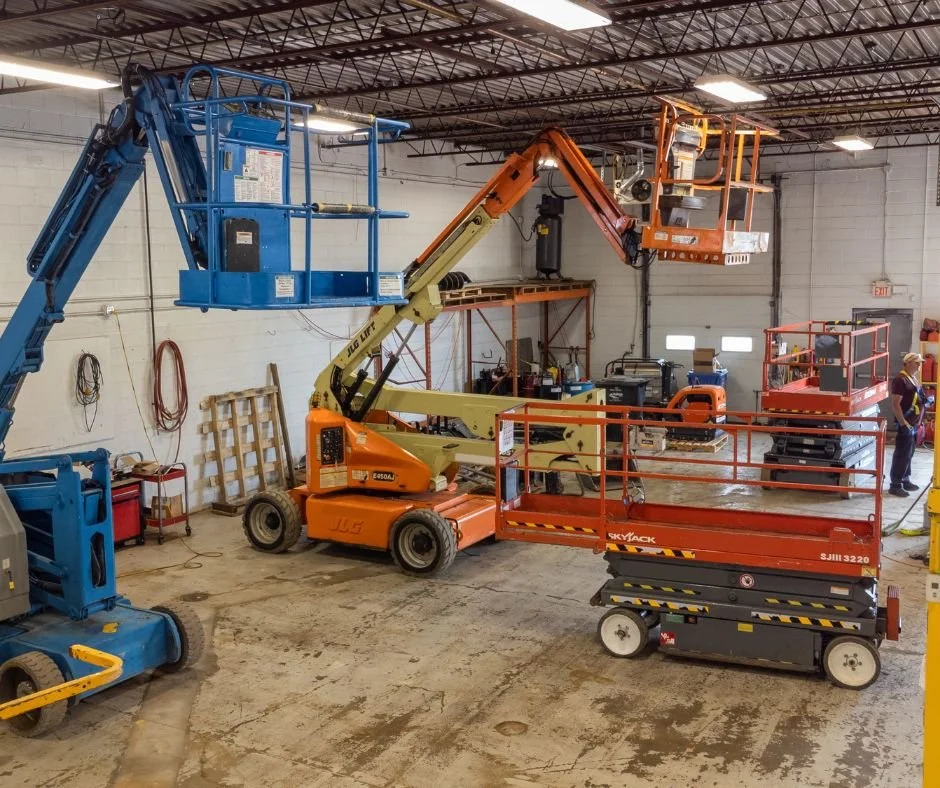
Aerial and Personnel Lifts
Since the early 70’s, the reach all terrain forklift has continued to evolve. Today they are a staple of almost every construction jobsite. When the backbone of the job site breaks down, the job slows down. Getting that equipment back up and running is on the top of everyone’s list. Milling Technologies understands this priority and will always do everything possible to get you back to making money as fast as possible. When you’re down, we are here to support you, after hours, weekends, even holidays. We have personnel on call 24/7.
Whether it’s troubleshooting an electrical issue, resealing a cylinder or a complete boom overhaul, we have the facilities and capabilities to complete the job. We have torn down, repaired or rebuilt just about every brand of reach forklift made. JLG is the largest manufacturer of reach forklifts. Milling Technologies is an JLG Service Center authorized to conduct warranty repairs on JLG, LULL, SKYTRAK, and GRADALL reach forklifts.
Annual inspections are no longer a luxury, but a necessity. By having an annual inspection conducted, a possible injury or a major component failure could be prevented. Planning for an upcoming major repair is easier when you have time to forecast and plan for it instead of trying to react to an emergency situation. Making sure all the safeties are in place and working can be a game changer if an accident were to happen.
Our field service can assist in almost any repair however; some jobs are just better done in a shop. We can weld cracks, remove and reseal most any cylinder on a reach forklift. Most hoses can be made and replaced on site as well.
Routine service can be an equipment owner’s best line of defense against downtime. In today’s market, profit margin is minimal and looking at service intervals as a cost is the wrong way to look at it. Routine services is a proven way to reduce equipment failures. Worn pins and bushings, linkage, clogged filters are extremely cheap to prevent or delay. These simple repairs can become very costly when neglected and takes time to repair due to possible machining for a quality repair.
When you need parts being a JLG service center we buy parts direct from the OEM so there is no double markup on our parts. We also continually strive to increase our parts inventory, to improve our support response time to our customers.
Consulting
If you are looking at purchasing a used forklift, beware of what your buying. The Internet makes it easy to find and purchase equipment. However, don’t make quick decisions based on limited information that can be easily manipulated. We can go to the unit and inspect it, take pictures and give a detailed written report. This way you have more information just a couple pictures and a sales pitch to make a decision with. We have conducted this service for customers as far away as Indonesia and several throughout the state.
Batteries
Batteries are the power of the machine, we have been called so many times to units that were not operating correctly to find the batteries were in a state discharge or terminals were so corroded that there current flow was greatly impeded or stopped all together. As a battery is used, it looses some of its water. This rate rapidly increases during the heat of the Florida summers. Proper battery maintenance is an absolute must to obtain maximum life. We also find that often instead of installing the proper number of 6 volt batteries in a unit someone will go to a discount store and purchase couple 12 volt batteries. This is extremely unsafe, the batteries weight are figured into the ballast of the lift. Installing fewer lighter batteries will result in a unit that is more prone to tipping. You do not have to use OEM batteries but they should be of equal weight and amperage capability for proper machine operation and safety. Also the chargers installed on these units are for a certain type battery, installing the wrong batteries can also cause damage to the charger as well.
Smaller personnel lifts are extremely common in today's construction, production and maintenance industries. Their list of uses continues to grow as they are developed and advanced through industry needs. The number of personnel lifts in service throughout these industries steadily rise. However, for the service industry these lifts have not kept pace. They are normally a low maintenance piece of equipment. Due to this they are often overlooked for routine inspections and preventative maintenance programs. When they do fail, they are often put back into service with field expedient repairs. Several years ago this was an acceptable practice. Today, liability issues and electronics means field expedient repairs are not the wise or logical way to repair modern equipment.
Scissor lifts
These units are most commonly indoor type units but are also popular in their off road outdoor version as well. Both units are usually neglected and receive poor maintenance but can slow a million dollar job. Given the cost of new machines today, a effective proactive maintenance program can keep your unit running and your job profitable while also increasing its resale value.
Stock Pickers/ Personal Lift
These lifts fall into a new but rapidly growing category. Due to insurance and OSHA pushing to eliminate the step ladder in the work place and new construction sites these units becoming ever popular. These units are either self-propelled or moved by hand and lift to a height of 12 ft. Like anything else, when they are down they are holding work up. Proper maintenance of these units are just as important as a unit that lift 3 people 150 ft.
Annual Maintenance
A unit very seldom fails when it is not needed. It has been shown numerous times that a simple and effective preventative maintenance program is the cheapest money spent on equipment. Having your equipment inspected annual is required by ANSI, recommended by almost every manufacturer, and makes good sense. Having a qualified mechanic inspect and perform an annual service on your machine can prevent many costly repairs. He can also greatly assist if a accident should occur where we find so many times where operational and safety decals have been removed or damaged beyond legibility that may have help to avoid an accident. Corrosion is also another common issue we find. The natural process of using the machines creates a corrosive vapor, especially during heavy long use. These vapors will corrode connections, terminal ends etc which impedes the transfer of full voltage. This reduced voltage over time can reduce the lifespan of several electrical components. In the Florida summers this process is accelerated.
Reconditioning
If you own or recently bought a used machine, we can bring life back into it for much less than the cost of a new machine. We can inspect and quote multiple levels of reconditioning with warranty. From repairing items in need and ensuring all safeties are in place to completely dismantling replacing all common wearable parts with sandblasting and painting the unit giving a like new appearance.
Contact us.
katie@millingtech.com
(352) 315-0585
2630 US Highway 27/441
Fruitland Park, FL 34731